
The rapid change in technology and the development of the Internet has changed the traditional definitions of manufacturers, suppliers, and customers. Supply Chain Management (SCM) is the integration of key business processes that add value for customers and other stakeholders. This added value is created through the integration of networks of suppliers that provide products, services, and information. Supply chain management allows this network of cooperating agents to perform one or more supply chain functions, potentially reducing costs and resulting in a competitive advantage for the organization.
The above figure illustrates the movement of products through a supply chain network. The supply chain begins when suppliers send raw materials to a factory. The factory may use the materials in a number of ways. They can either manufacture subcomponents or assemble the materials into finished products to be sent to the warehouse or distribution center where customers can get the products.
In order for the supply chain to be successful, organizations must recognize that they are but one player in the long chain that starts with suppliers and also includes transporters, distributors, and customers. The organizations must interact cooperatively with their channel partners (Gandhi, 2003). An important issue relating to the development of a collaborative supply chain is following specified ordering and replenishment policies. An example of Collaborative Supply Chain Planning (CSCP) is Vendor Managed Inventory (VMI).
Vendor Managed Inventory allows the supplier to receive electronic data to maintain constant information about the manufacturer’s sales and stock levels. The supplier is then responsible for creating and managing the inventory replenishment schedule. VMI is defined as a process where the supplier generates orders for customers based on demand information sent by the customer (Gandhi, 2003). VMI leads to changes in both the buyers’ and suppliers’ inventory management activities. VMI has not become a standard way of managing the replenishment process in the supply chain due to some practical issues that have slowed down its implementation in many organizations. One problem may exist because the supplier and manufacturer are unwilling to share information because of a lack of trust. In order for VMI to be effective, it has to produce observable benefits, especially in the reduction of inventory costs.
Some of the benefits of VMI include:
- lower customer inventories
- better forecasts
- reduced costs
- improved services
- strengthening competitive advantage
- strengthening buyer-supplier relationships
Similar to SCM and VMI, Collaborative Planning, Forecasting, and Replenishment (CPFR) was developed to allow better communication of control information, which enables coordination and optimization of shared business processes. CPFR is defined as an initiative among all participants in the supply chain intended to improve the relationship among them through jointly managed planning processes and shared information (Seifert, 2003). When successful, it also improves relationships between producers and retailers.
One of the first CPFR projects was initiated by Wal-Mart and Warner-Lambert, which merged with Pfizer in 2000. This project was intended to reduce inventories across the supply chain. It provided comparisons of sales and order forecasts of each trading partner and highlighted any visible forecast differences early enough for the partners to resolve any potential issues. Warner-Lambert applied CPFR to the Listerine mouthwash products by sharing of forecasts and responding to inconsistencies between the collaboration partners’ forecasts. In Warner-Lambert’s case, Wal-Mart’s promotions created large swings in consumer demand, which Warner-Lambert was unaware of prior to CPFR. Warner-Lambert maintained substantial inventory as a hedge in order to prevent supplies from running out of stock. Wal-Mart and Warner-Lambert independently calculated the demand they expected six months in advance. The partners shared this information, as well as the weekly forecast, and they worked together to resolve variations between their forecasts on a weekly basis. Wal-Mart began placing orders six months in advance, instead of nine days, so that Warner-Lambert was able to construct a smoother production plan. This allowed Warner-Lambert to maintain production based on consumer demand for Listerine rather than maintaining sufficient stock. Wal-Mart’s in-stock position improved and sales increased, while inventories dropped. Additionally, Warner-Lambert’s supply management improved substantially. Optimal applications of CPFR occur when, for example, many other retailers join Wal-Mart in sharing their projected demand with Warner-Lambert. Combining demand forecasts from many retail customers makes it possible for Warner-Lambert’s production plans to be much better aligned with total market demands.
Benefits of using CPFR are:
- drastically improved reaction times to consumer demand
- higher precision of sales forecasts
- direct and lasting communication
- improved sales
- inventory reduction
- reduced costs
The CPFR process model is divided into three phases: planning, forecasting, and replenishment. The figure below provides an overview of the phases and activities in the CPFR model.
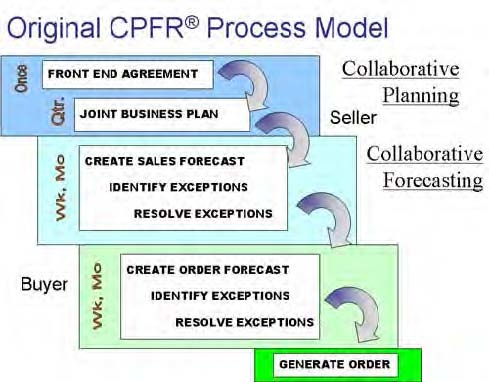
Planning consists of identifying an opportunity for collaboration, then developing an agreement to collaborate, as well as forming a collaborative business plan. Forecasting is the most important part of the model. It provides the mechanism through which needs are determined. It is improvement of this aspect of the supply chain through which all of these strategies provide advantages over more traditional methods. Replenishment involves making and delivering the product consistent with the needs schedule developed by the forecast. More accurate forecasts lead to production of only the needed products, which smooths the production schedule and results in price stability. This allows for existing capacity to be used to enable other products or to develop markets for additional production.
Many of the processes replaced by SCM, VMI, and CPFR strategies involve merely producing “the average of this month over the last 3 threes plus a small percentage”. Such ad hoc strategies, although widely employed, contain substantial inefficiencies. Exploiting these inefficiencies is the incentive for pursuing these programs. Another reason such programs are popular with managers is that savings realized go directly to the bottom line as customer needs are met while using less organizational resources.
An effective supply chain management program is one that develops processes shared among all the supply chain members in order to minimize the waste of time and enable fast and reliable reactions to changes in demand. Technology has exponentially increased the transfer of information between organizations, resulting in improved supply chain performance. Two common practices, Just-In-Time (JIT) and agile inventory approaches, are used to allow suppliers to react more quickly to changes in customer demand.
Just-In-Time emphasizes minimizing inventory and smoothing the flow of materials to ensure adequate and prompt delivery of components. Products and materials are ordered and delivered “just in time” as they are needed reducing inventory costs and ensuring unneeded materials are not ordered. JIT began at Toyota Motor Company but it evolved into a system for continuous improvement of all aspects of the manufacturing operations.
Lean production is a philosophy based upon a collection of management methods and techniques (Russell, 2006). Workers and machines are multifunctional in lean systems. Workers are required to perform various tasks and help in the improvement process. The machines are arranged in small, U-shaped work cells; this structure enables parts to be processed in a continuous flow. Workers produce parts one at a time and transport them between the cells in small lots. The only schedules prepared are for the final assembly line. This schedule “pulls” sub-components through production by making requests to stations that cascade to production lines. Nothing is done until requested by the next station.
The system is best implemented when suppliers are few in number and are reliable. The suppliers’ manufacturing system must be flexible, because multiple deliveries may be requested of the same item in the same day. Lean production produces items in necessary quantities at necessary times. Consequently, quality must be extremely high, as there is little buffer inventory between workstations and production schedules include only requested products.
Lean systems can produce high quality service quickly at a low cost. Also, the system responds to changes in customer demand. Many retailers use lean systems such as Zara and Blockbuster.
Benefits of using lean production are:
- reduced inventory
- improved quality
- lower costs
- reduced space requirements
- shorter lead time
- increased productivity
- greater flexibility
- better relations with suppliers
- simplified scheduling and control activities
- increased capacity
- better use of human resources
- greater product variety
- 3000 reads