
As mentioned in the previous section equipment operates in a linked and complex environment. So it is necessary to pay attention beyond the performance of individual tools towards the performance of the whole factory. According to Scott and Pisa1, the answer to this requirement is the OFE metric, which is about combining activities and relationships between different parts of the equipment, and integrating information, decisions, and actions across many independent systems and subsystems. The problem is that a specific and unique method to calculate OFE does not exist. There many methodologies and approaches, with different level of complexity, different information coming from and different lacks.
A first common-sense approach is to measure OEE at the end of the line or process. Following this approach we can see OEE as
|
and
|
Here OEE measures effectiveness in term of output that is easy to be taken out at factory level too. So OFE becomes:
|
It is not always ideal. The complexity of OEE measurement arises where single or multiple sub-cells are constrained by an upstream or downstream operation or bottleneck operation. The flow is always restricted or limited by a bottleneck operation, just as a chain is only as strong as its weakest link. So according to Goldratt2 we can measure OEE in real time at the bottleneck. Any variations at the bottleneck correlate directly to upstream and downstream process performance. Huang et al.3 proposed a manufacturing system modeling approach, which captures the equipment interconnectivity information. It identifies four unique subsystems (series, parallel, assembly and expansion) as a basis for modeling a manufacturing system, as shown in Figure 2.3.
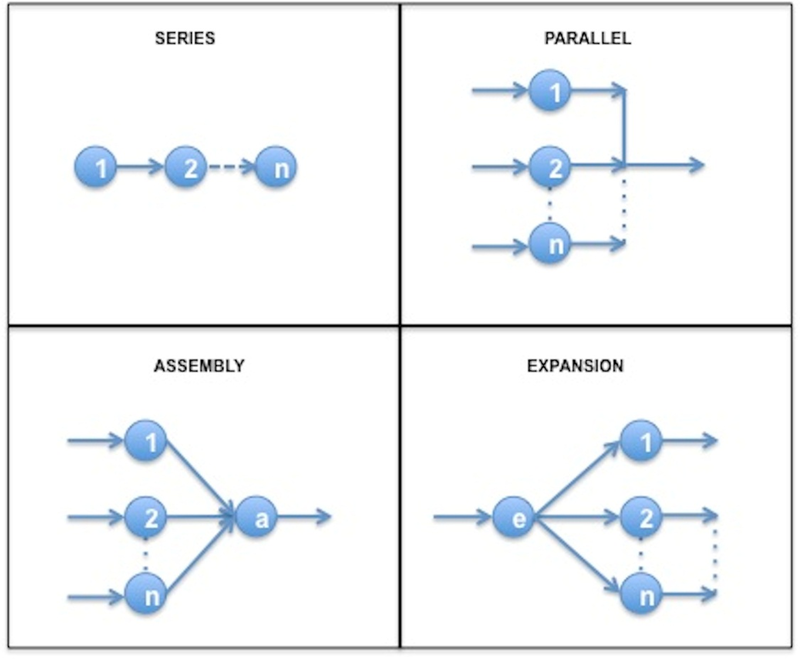
Muthiah et al.4 developed the approach to derive OTE metrics for these subsystems based on a “system constraint” approach that automatically takes into account equipment idle time.
Other methods are based on modeling the manufacturing systems. Some of these notable approaches are queuing analysis methods5, Markovian methods6, Petri net based methods7, integrated computer-aided manufacturing definition (IDEF) method8, and structured analysis and design technique (SADT)9. In addition to them there are several commercial tools that have been reviewed and categorized by Muthiah and Huang10.
- 2912 reads