
OEE provides simple and consolidated formulas to measure effectiveness of the equipment or production system. Moreover Dal et al.1 point out that it can also be used as an indicator of process improvement activities since OEE is directly linked to the losses as well as OEE can be even used to compare performance across the factory highlighting poor line performance or to quantify improvements made2. Moreover improving can be pursued by:
- Backtracking to determine what loss reduces effectiveness.
- Identifying bottlenecks as not only the slowest machine, but as the machine both slower and less effective.
All these goals need of an approach based on the Deming Cycle3. It is an improvement cycle to increase the plant OEE rating until the target goals and world class manufacturing status are achieved ( Figure 2.4 )
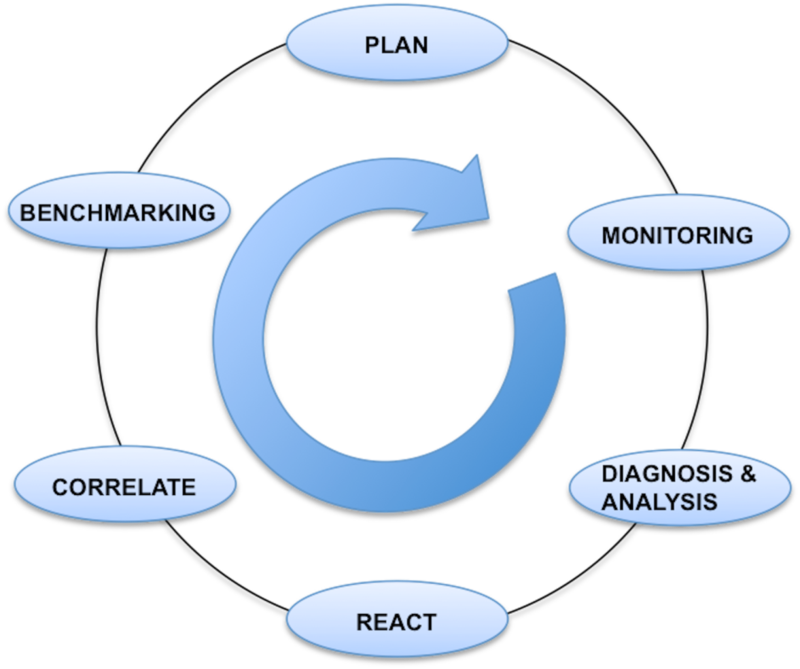
This approach requires a large amount of data that can be provided both in a static or dynamic way. In the first case data are picked up only at the end of a certain period and used in the Diagnosis & Analysis stage.
There is another way to use OEE and it is to know exactly what is happening in real time through a continuous monitoring to immediately identify possible problems and react in real-time using appropriate corrective actions. Information on OEE items (maintenance and operational equipment effectiveness, product data accuracy, uptimes, utilization, bottlenecks, yield and scrap metrics, etc.) is really valuable in environments where making decisions in near real-time is critical. This second approach requires then a data collection system completely automatized and moreover the Diagnosis & Analysis stage should be automatic.
In the next sections we will take into consideration different strategies to acquire data and we will illustrate main automated tool for the OEE integration.
- 2832 reads