
At this point in the SDLC, we have completed the systems analysis phase (the systemssurvey and structured systems analysis). We have also completed the systems design phase by selecting hardware and software (systems selection) and by preparing the systems design and the implementation plan (structured systems design). It is time to install and begin to use our new or modified system.
Review Question What is systems implementation? |
Systems implementation is a set of procedures performed to complete the design (as necessary) contained in the approved systems design document and to test, install, and begin to use the new or revised Information System. Figure 7.1 depicts systems implementation as the fifth major step in the development of an Information System.
The systems implementation goals are as follows:
- Complete as necessary the design contained in the approved systems design document.For example, the detailed contents of new or revised documents, computer screens, and database must be laid out and created.
- Write, test, and document the programs and procedures required by the approvedsystems design document.
- Ensure, by completing the preparation of user manuals and other documentationand by training personnel, that the organization’s personnel can operate the newsystem.
- Determine, by thoroughly testing the system with users, that the system satisfies theusers’ requirements.
- Ensure a correct conversion by planning, controlling, and conducting an orderly installationof the new system.
Review Question What are the systems implementation goals? |
In this section we describe implementation approaches that can be taken to install the new or modified system. Figure 7.2 depicts the three most common implementation approaches.
Review Question What are the three major approaches to implementing an Information System? |
Figure 7.2(a), the parallel approach, provides the most control of the three. In the parallel approach, both the old and new systems operate together for a time. During this period, time x to time y (which is usually one operating cycle, such as one month or one quarter), the outputs of the two systems are compared to determine whether the new system is operating comparably to the old. At time y, management makes a decision, based on the comparison of the two systems’ outputs, whether to terminate the operation of the old system. The parallel approach provides more control because the old system is not abandoned until users are satisfied that the new system adequately replaces the old. Although this approach makes good intuitive sense, in practice it frequently alienates users who perceive parallel operations as doubling their workload.
![]() |
Figure 7.2(b), the direct approach, is often called the “Big Bang” approach and is the riskiest of the three approaches. At time x the old system is stopped and the new system cuts in with no validation that the new system operates comparably to the old. While we will see a little later that it need not be so, enterprise systems are often implemented using this approach. Sometimes, as you’ll see in the Hershey story in Chapter 11, direct implementations can lead to disaster. |
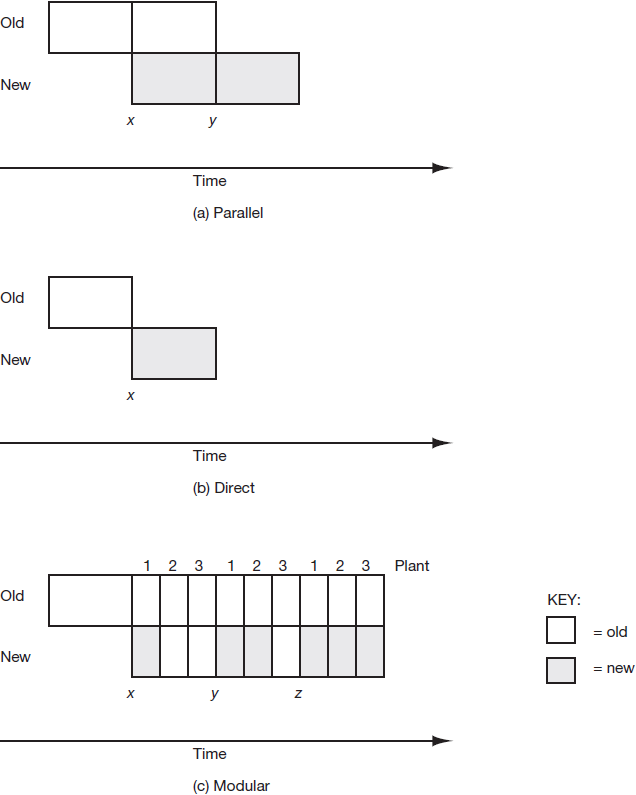
Figure 7.2(c), the modular approach, can combine parallel or direct approaches to tailor the implementation to the circumstances. With the modular approach, the new system is either implemented one subsystem at a time or is introduced into one organizational unit at a time. For example, a new Order-to-Cash system could be implemented by first changing the sales order preparation and customer inquiry portions, followed by implementing the link to the billing system, followed by the link to the inventory system. Figure 7.2(c) depicts the gradual implementation of a new system into three organizational units. A new payroll system is installed for the employees of plant 1 at time x, followed by plant 2 at time y, and finally by plant 3 at time z. Implementation at any plant could be direct or parallel. Modular implementation permits pilot testing of a system or system component and elimination of any problems discovered before full implementation.
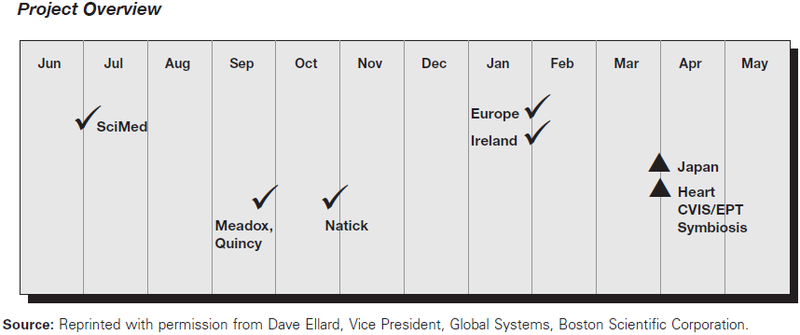
![]() |
Figure 7.3 depicts the modular schedule used at the Boston Scientific Corporation to implement SAP at all of its worldwide divisions and locations. As shown in this example, several installations were complete while two more were scheduled for the end of March. At Boston Scientific, several members of the project team were on location on each worldwide “go-live” date to provide assistance, ensure consistency of all implementations, and to learn and provide improvements for subsequent implementations. |
- 32702 reads