
At the beginning of this chapter, the inventory system was described as the buffer, or shock absorber, for the production function; the logistics subsystem performs the same role for the marketing function. The necessary raw materials are put into the raw material inventory (RMI). As needed, they are transferred to the work-in-process (WIP) inventory, and upon conversion into finished products, they are stored in the finished goods inventory (FGI). This buffering system of successive inventories, combined with an equally well-run logistics system, is every manager's paradise. No machine runs out of raw materials, and no retailer faces stockouts because of breakdowns in the production process.
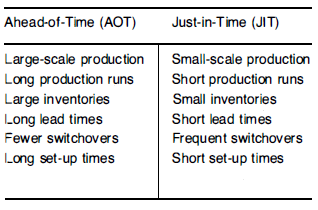
This smoothing of the purchasing-production-delivery chain, however, is achieved at very high inventory cost. The large fixed investment for space and equipment and the large inventory carrying costs associated with this "comfortable" production strategy have created a great demand for new and creative ways of trimming material and product handling costs.
The Japanese "just-in-time" (JIT) scheme has been heralded as the most innovative and efficient method of lowering material and finished goods handling costs. 1 Figure 13.8 compares the conventional Western "ahead-of-time" (AOT) system to the "just-in-time" scheme. JIT is characterized by smaller production runs, frequent changes in the production set-up, and closely synchronized operations, which transform raw materials into fabricated parts, fabricated parts into subassemblies, subassemblies into finished goods, and finished goods into sales. In order for JIT to be less costly, there must be a way of making up for time lost as a result of the frequent set-ups. In addition, there must be a way of ensuring the timely arrival of the needed materials or parts. In other words, external disturbances such as changes in vendors' schedules must be internalized and problems internal to the production line must be externalized. These principles are the key to the success of JIT. Good relationships with external vendors convert them into "family" members, and changes in the assembly line that are necessary for the new set-up are performed "externally" ( that is, while machines are running) so as not to interrupt the flow of production.
In very simple terms, the main idea behind JIT is to purchase, produce, and deliver finished goods just in time to be sold, subassemblies just in time to be assembled into finished goods, fabricated parts just in time to go into subassemblies, and raw materials just in time to be transformed into fabricated parts. 2 The JIT philosophy evolved from the need to reduce production costs, eliminate waste, and recognize workers' abilities. The objectives of the JIT system are
- To minimize the work-in-process (WIP) inventory
- To minimize fluctuations in WIP so as to simplify inventory controls
- To minimize production instability by preventing fluctuations in demand from one process to another
- To provide better control by decentralizing process supervision and moving it to the shop floor
- To reduce defects
The main elements of JIT are
- A focused factory
- Reduced set-up times
- Group technology
- Total preventive maintenance
- Cross-trained employees
- Uniform work loads
- Just-in-time delivery of purchased parts and/or components
- Kanban
The focused factory concept requires that the production system be specifically designed for a limited number of product lines.
Reduction in set-up time is critical to the JIT philosophy. In order for production of parts in small lots to be economically feasible, set-up times must be short. The JIT approach requires that a set-up take less than ten minutes. The following four strategies comprise the Japanese approach to reducing setups:
- Separate internal set-ups from external set-ups, internal set-ups being those that cannot be done while a machine is running and external setups being those that can.
- Convert internal set-ups to external set-ups whenever possible.
- Eliminate the adjustment process. Adjustments to machines usually take 50 to 70% of the total set-up time; minimizing adjustment time is therefore critical.
- Abolish the set-up step whenever possible. Standardize parts within and across product lines or produce various parts on small, rather than large, machines.
Group technology is an engineering and manufacturing philosophy that emphasizes "sameness' in parts, equipment, and processes. Machines are grouped according to the destination of the parts they produce rather than according to their function.
Given the interdependence of work centers in a JIT system, a machine malfunction can necessitate the shutdown of an entire line (a problem magnified by the lack of buffer stock between work centers). Thus preventive maintenance is critical. Japanese workers are very knowledgeable about their machines' maintenance needs and are trained to do many repairs themselves.
Because only required items are produced in a JIT system, machines may become idle. Therefore, workers are cross-trained so that they can be moved to other machines. In addition to increasing efficiency, this practice lessens the monotony and boredom that characterize the traditional assembly line.
If products and components are to be produced at, or close to, the market rate by a limited number of work centers, uniform work loads must be established. Production of the same product mix daily ensures a smooth supply of products and components.
Purchased parts are delivered to the assembly area just in time for assembly into the finished products. More frequent deliveries of raw materials and purchased components reduce the amount of inventory needed, and therefore the space used for storage, and increase production flexibility. JIT deiivery requires that businesses maintain good relationships with vendors and share information with vendors and customers.
Finally, kanban refers to a visible record, typically in the form of a card, that authorizes production and/ or transfers parts from one work center to another.
- 2400 reads